Navigating the Challenges of Outsourcing Packaging: Best Practices for Success
Baraka • November 12, 2024
Navigating the Challenges of Outsourcing Packaging: Best Practices for Success
Introduction
In an increasingly globalized world, companies are constantly seeking ways to optimize their operations. One trend that has gained traction is outsourcing, especially in the area of packaging. But why is packaging so important in the supply chain? Simply put, it not only protects the product but also plays a crucial role in customer perception. In this article, we will explore the common challenges companies face when outsourcing their packaging processes and offer best practices for successfully navigating these obstacles.
Common Challenges in Packaging Outsourcing
Quality Control
One of the biggest challenges when outsourcing packaging is maintaining adequate quality control.
Risks Associated with External Suppliers
When working with third parties, there is always a risk that they may not meet established standards. Problems in this area can lead to costly recalls and irreparable damage to reputation.
Confidentiality and Data Protection
Security is another critical aspect. Companies must ensure that their confidential data is protected. This involves establishing clear agreements on how sensitive information will be handled.
Communication Management
Effective communication is vital for any business relationship, but it can be a challenge when working with external suppliers.
Language and Cultural Barriers
Cultural and language differences can create misunderstandings. Therefore, it is essential to establish clear channels from the outset.
Supplier Dependence
Excessive dependence on a single supplier can be risky. If they encounter operational or financial issues, your company could be adversely affected.
Consequences of Lack of Alternatives
It’s essential to have a plan B. Considering multiple suppliers can help mitigate this risk.
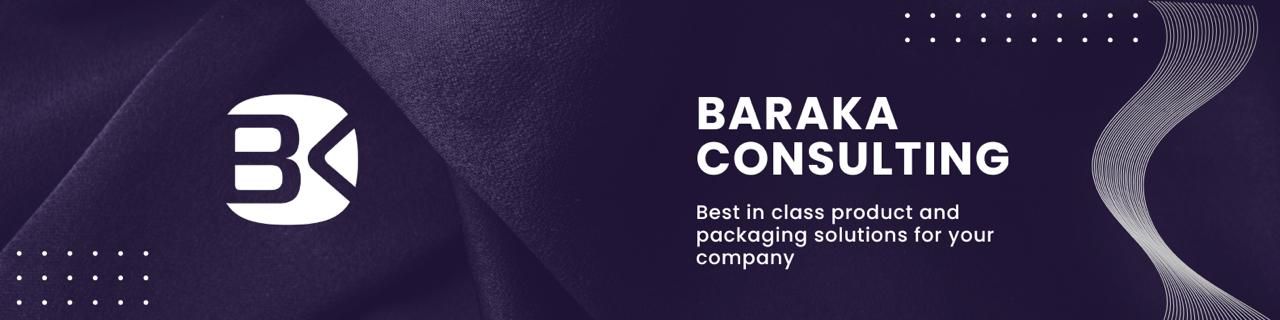
Best Practices to Overcome Challenges
Careful Selection of the Supplier
Choosing the right supplier is crucial.
Evaluation Criteria
Research their experience, reputation, and technical capability. A reliable supplier can make a significant difference.
Establishing Clear Agreements
Contracts should be detailed and specific.
Contracts and Expectations
Clearly define expectations from the beginning. This includes deadlines, quality standards, and procedures in case of non-compliance.
Constant and Effective Communication
Maintaining open communication is key to avoiding misunderstandings.
Recommended Tools and Methods
Use digital tools such as collaborative platforms or messaging applications to facilitate daily communication.
Continuous Monitoring and Evaluation
It’s not enough to establish agreements; it’s also important to monitor compliance.
Key Performance Indicators (KPI)
Define clear KPIs to evaluate supplier performance. This will allow you to make adjustments if necessary.
The Role of Technology in Outsourcing
Technology plays a fundamental role in optimizing the process.
Technological Tools for Packaging Management
From specialized software to automated systems, there are many tools available that can facilitate packaging management.
Innovations that Facilitate Collaboration
Digital platforms allow for smoother collaboration between companies and suppliers, thus improving overall efficiency.
Success Stories in Packaging Outsourcing
There are numerous companies that have achieved great results through outsourcing.
Examples of Successful Companies
Companies like Coca-Cola have effectively utilized outsourcing strategies for their packaging, thereby improving their operational efficiency.
Lessons Learned
These cases demonstrate that careful supplier selection and effective communication are essential for maximizing outsourcing benefits.
Future Trends in Packaging Outsourcing
The future promises to be exciting for those involved in this practice.
Sustainability in Packaging
More and more companies are seeking sustainable solutions. This not only meets consumer expectations but also complies with stricter environmental regulations.
Automation and Digitalization
Digitalization is transforming how logistical processes are managed. Automation can further enhance efficiency by reducing human errors.
Conclusion
Navigating the challenges of packaging outsourcing can be complicated, but with the right best practices, companies can successfully overcome these obstacles. From carefully selecting suppliers to maintaining clear and constant communication, every step counts. Effective implementation not only improves the quality of the final product but also strengthens long-term business relationships.
What is packaging outsourcing?
It is a strategy where companies hire third parties to handle their packaging processes, allowing them to focus more on their core competencies.
What are the main challenges when outsourcing packaging?
Challenges include maintaining quality control, protecting confidential data, managing effective communications, and avoiding excessive dependence on a single supplier.
How do I select a good supplier?
Research their experience, reputation, and technical capabilities. It’s important to choose a reliable supplier with a proven track record.
What technologies are useful in outsourcing?
Digital tools such as specialized software for logistics management and collaborative platforms are essential for facilitating efficient processes.
What are future trends in packaging?
Trends include increasing focus on sustainable solutions and technological advancements such as automation and digitalization.