Understanding Value Stream Mapping in Packaging: A Comprehensive Guide
Baraka • November 12, 2024
Understanding Value Stream Mapping in Packaging: A Comprehensive Guide
Introduction
In an increasingly competitive business environment, companies are constantly seeking ways to optimize their processes. One powerful tool that has gained popularity is Value Stream Mapping (VSM). But what exactly is it? VSM is a technique that allows you to visualize and analyze all the steps necessary to take a product from conception to final delivery. In this guide, we will delve into how this tool can transform the packaging industry.
Benefits of Value Stream Mapping in Packaging
Identification of Waste
One of the main advantages of VSM is its ability to identify waste in processes. By mapping each step, you can clearly see where resources are being used unnecessarily. This not only saves money but also improves efficiency.
Improvement of Operational Efficiency
VSM enables companies to identify bottlenecks and delays. By addressing these issues, operational efficiency can be significantly increased. Imagine being able to shorten wait times and reduce operational costs; this is possible with effective mapping.
Increase in Customer Satisfaction
When you optimize your processes, you not only benefit your company; you also enhance the customer experience. A faster and more efficient flow means your customers will receive their products more quickly, leading to greater satisfaction.
Key Elements of Value Stream Mapping
Symbols and Notations Used
VSM uses standardized symbols to represent different processes and flows. Familiarizing yourself with these symbols is essential for creating effective maps. For example, a rectangle may represent a process, while an arrow indicates the flow between processes.
Material and Information Flows
It’s crucial to understand both physical flows (materials) and informational flows (data). A good map should show how materials move through the process and how information flows between departments.
Important Metrics to Consider
When creating a map, there are several metrics you should keep in mind, such as cycle times, wait times, and inventory levels. These metrics will help you assess current effectiveness and set goals for future improvements.
Steps to Create a Value Stream Map
Define the Scope of Mapping
Before starting, it’s important to clearly define which part of the process you will map. This can include everything from receiving raw materials to delivery to the customer.
Selection of the Product Family
Deciding which specific family or group you will map will allow you to focus better on similarities between products or services.
Document the Current State
This step involves observing and recording each current stage of the process. Accurate data collection is fundamental here.
Data Collection and Observations
Go out onto the production floor and observe how materials and information actually flow. Talk to employees to gather valuable insights about potential inefficiencies.
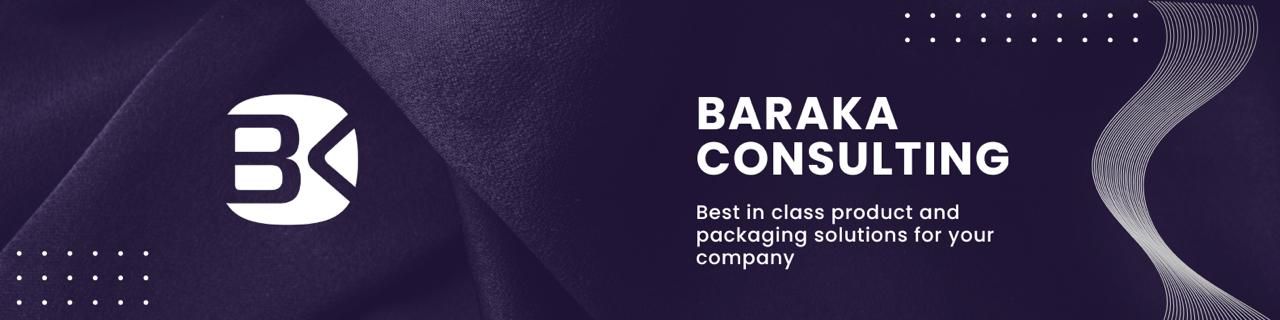
Identify Areas for Improvement
Once you have your current map, it’s time to analyze it. Look for bottlenecks or areas where significant waste occurs.
Analysis of Bottlenecks and Waste
Ask yourself where things slow down or where time is wasted unnecessarily. This information will be key for designing effective improvements.
Design the Future State
Based on your analysis, create a map that represents how the process should ideally function.
Establishing Clear Objectives
Define what changes you want to implement and how you will measure their success. This will help keep you focused throughout the process.
Common Challenges in Value Stream Mapping
Resistance to Change
People are often reluctant to change their habitual ways of working. It’s essential to address these concerns from the outset.
Lack of Accurate Data
Without accurate data, your maps may be incorrect or misleading. Always ensure you collect reliable information.
Limited Team Involvement
Mapping should be a collaborative effort. If only a few people are involved, you may miss valuable perspectives.
Best Practices for Effective Mapping
Involve the Entire Team
Make sure all relevant departments are represented in the process. This will enrich your map with different viewpoints.
Keep Visual Representation Simple
Don’t complicate your maps too much; they should be easy to understand and follow. Clarity is key.
Regularly Review and Update Maps
The business environment changes constantly; therefore, your maps should reflect these changes. Schedule regular reviews to keep them updated.
Success Stories in Using VSM in Packaging
Practical Examples in the Industry
Numerous companies have seen positive results after implementing VSM. For instance, a pharmaceutical company was able to reduce its total time by 30% after optimizing its processes through mapping.
Results Obtained and Lessons Learned
Successful cases demonstrate that careful implementation can lead to significant improvements in both efficiency and customer satisfaction.
Future Trends in Value Stream Mapping
Integration with Digital Technologies
Digitalization is changing how many business tasks are performed, including mapping. Digital tools can further facilitate this process.
Focus on Sustainability
As more companies seek to be sustainable, integrating sustainable practices within VSM will be key to meeting current expectations.
Conclusion
Value Stream Mapping is a powerful tool that can significantly transform processes within packaging. By identifying waste, improving operational efficiency, and increasing customer satisfaction, companies can better position themselves to compete in a challenging market. Implementing this technique not only benefits your organization internally but also enhances your relationship with customers by delivering faster and more efficient products.
What is Value Stream Mapping exactly?
It is a technique that allows you to visualize all the steps necessary to take a product from its creation to its final delivery to the customer.
What are the main benefits of VSM?
Benefits include efficient identification of waste, operational improvement, and an overall increase in customer satisfaction.
How are value stream maps created?
They are created by first documenting the current state through detailed observations and then designing a future state based on identified areas for improvement.
What challenges can be faced when implementing VSM?
Challenges include resistance to change from staff, lack of accurate data, and limited involvement from necessary team members for effective changes.
How can best practices be applied in VSM?
By involving all relevant team members, keeping visual representations simple, and regularly reviewing maps to ensure ongoing relevance.