Implement Quality Assurance System Packaging Process
Discover how to enhance your packaging process with a robust Quality Assurance System. Learn best practices, tools, and strategies to ensure product integrity, compliance, and customer satisfaction. Streamline operations, reduce errors, and elevate your packaging standards with our comprehensive guide.
Our Clients
We serve a wide range of clients and companies of different sizes, all across the world.
Implement Quality Assurance System Packaging Process
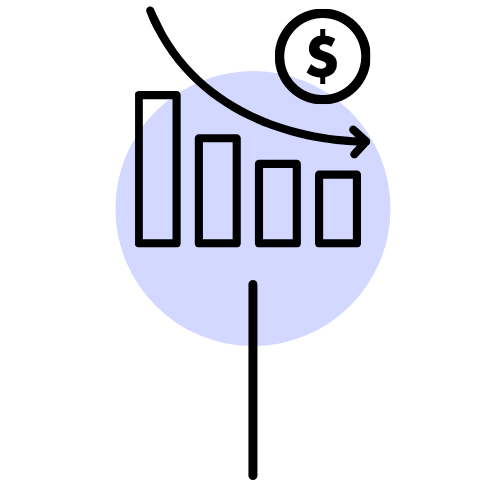
Product and Packaging
Maximization
We identify material and design standardization and optimization opportunities via benchmarking data and complexity analysis of your product, packaging and supply chain.
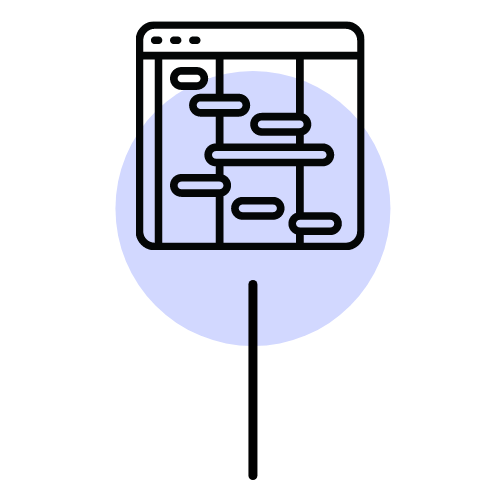
Technical Project Management
Our 15 years of experience in the consumer goods segment provides our clients first in class project management and technical mastery.
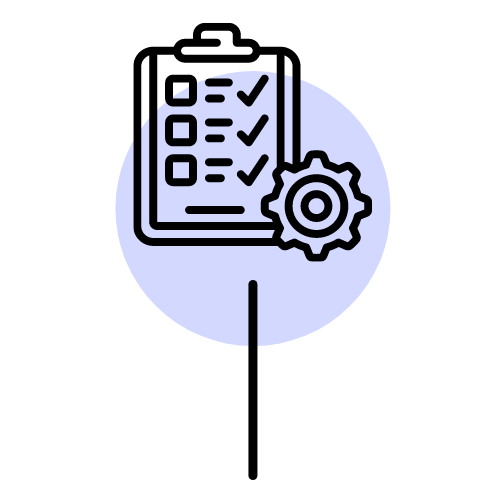
Standards and Quality Management Improvement
We help improve your technical specifications to drive more efficiency providing more control over quality systems.

Enhancing Packaging Process through Quality Assurance
Enhancing the packaging process through quality assurance involves implementing systematic measures to ensure that packaging meets predefined standards and specifications, thereby improving overall product quality and customer satisfaction. This approach focuses on identifying potential defects and inefficiencies in the packaging line, utilizing advanced technologies and methodologies such as automated inspections, real-time monitoring, and data analytics. By integrating quality assurance into every stage of the packaging process, companies can reduce waste, minimize errors, and ensure compliance with industry regulations. Additionally, this proactive strategy fosters continuous improvement, enabling businesses to adapt to changing market demands and maintain a competitive edge. Ultimately, a robust quality assurance framework not only enhances the efficiency and reliability of the packaging process but also strengthens brand reputation and consumer trust.
Quality Control Measures in Packaging
In conclusion, implementing a robust Quality Assurance (QA) system in the packaging process is essential for ensuring product integrity, customer satisfaction, and regulatory compliance. By integrating advanced technologies and standardized procedures, companies can effectively monitor and control each stage of the packaging process, from material selection to final inspection. This not only minimizes the risk of defects and recalls but also enhances operational efficiency and cost-effectiveness. Furthermore, a well-structured QA system fosters a culture of continuous improvement and accountability, empowering employees to contribute to the overall quality objectives. Ultimately, a comprehensive QA system in packaging not only safeguards the brand's reputation but also builds trust with consumers, paving the way for long-term success in a competitive market.
WHY CHOOSE US?
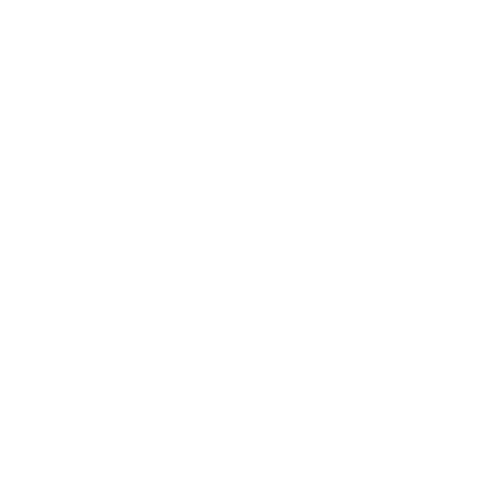
We analyze your product and packaging variables to create clear indexes on how you compare to your competition to help generate standardization and cost optimization options based on these findings.
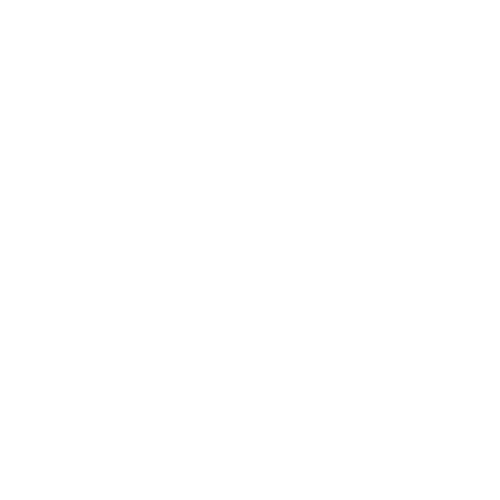
We help you to understand which are the best practices used inside your company and how your products and packages compare to the best practices in the market through external benchmarking.
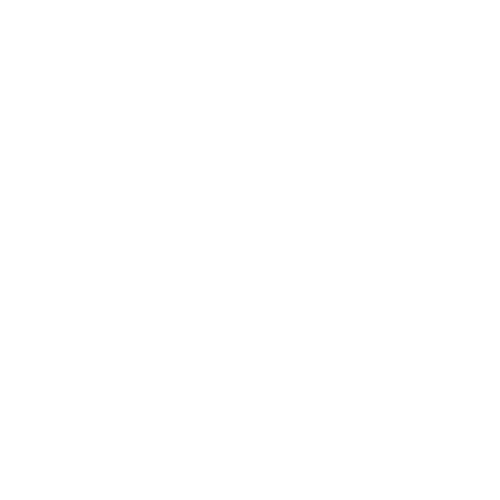
We focus on opportunities based on technical feasibility and size of the prize.
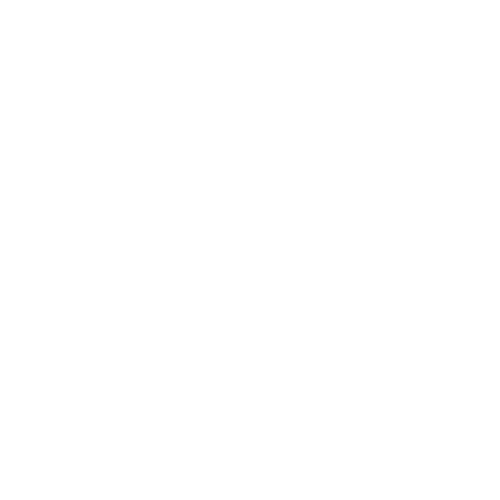
We have more than 15 years of experience working with consumer goods companies across different categories and regions. We provide access to a multi-functional team with technical mastery across different packaging and production platforms.
Meet Our Team
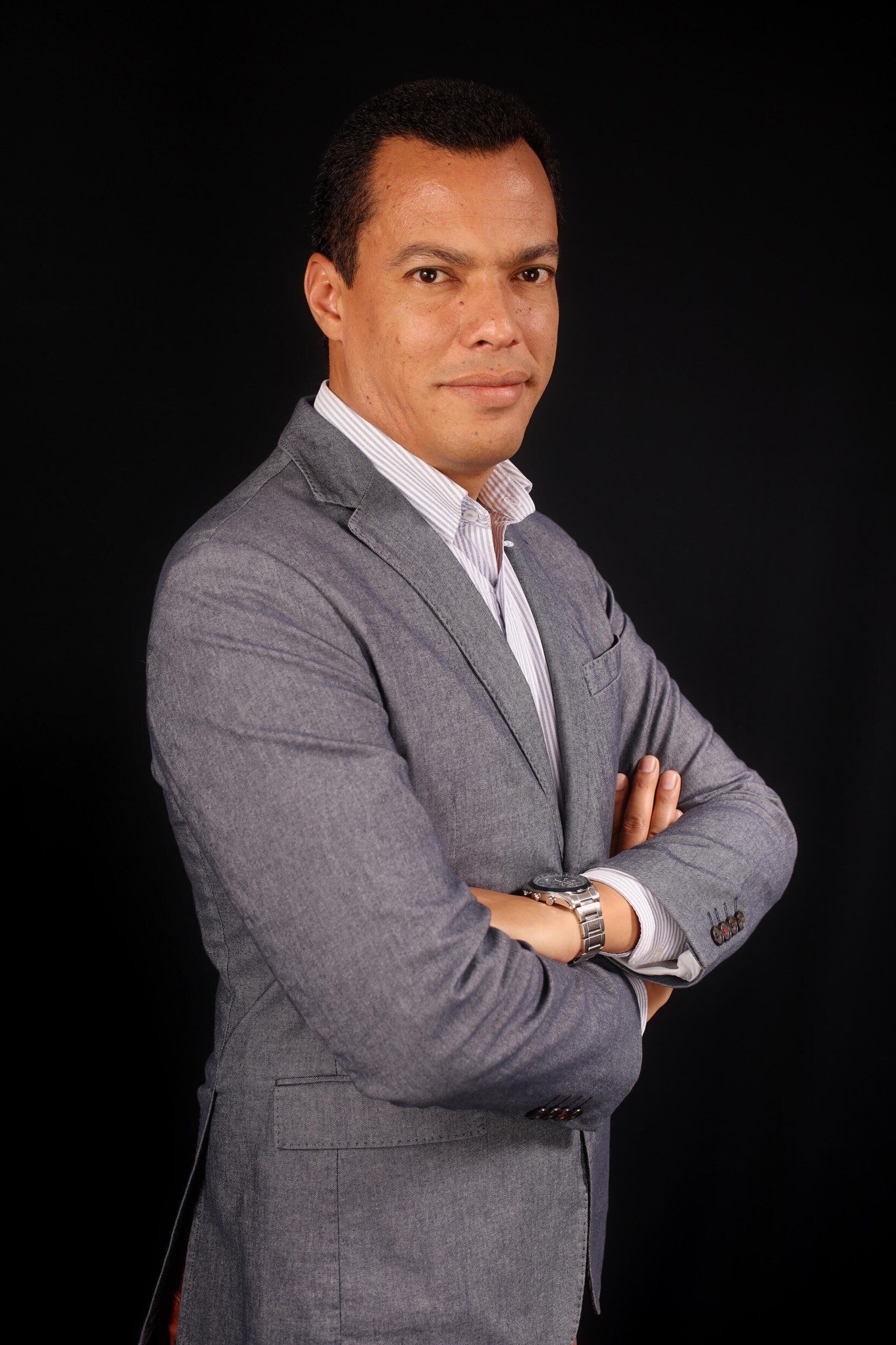
Victor Escalona
CEO AND CO-FOUNDER
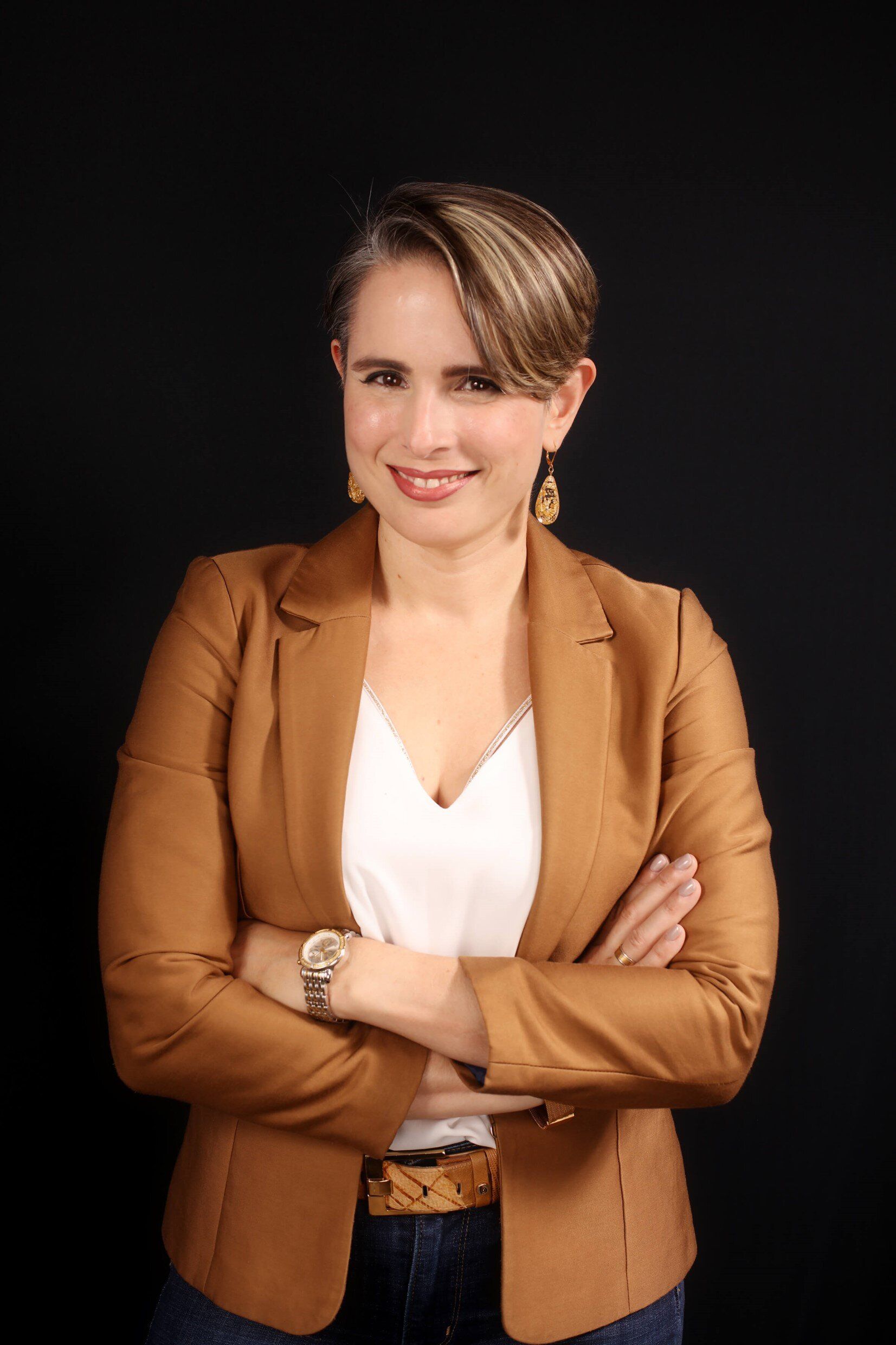
Carolina Chaparro
BUSINESS DELIVERY MANAGER AND CO-FOUNDER
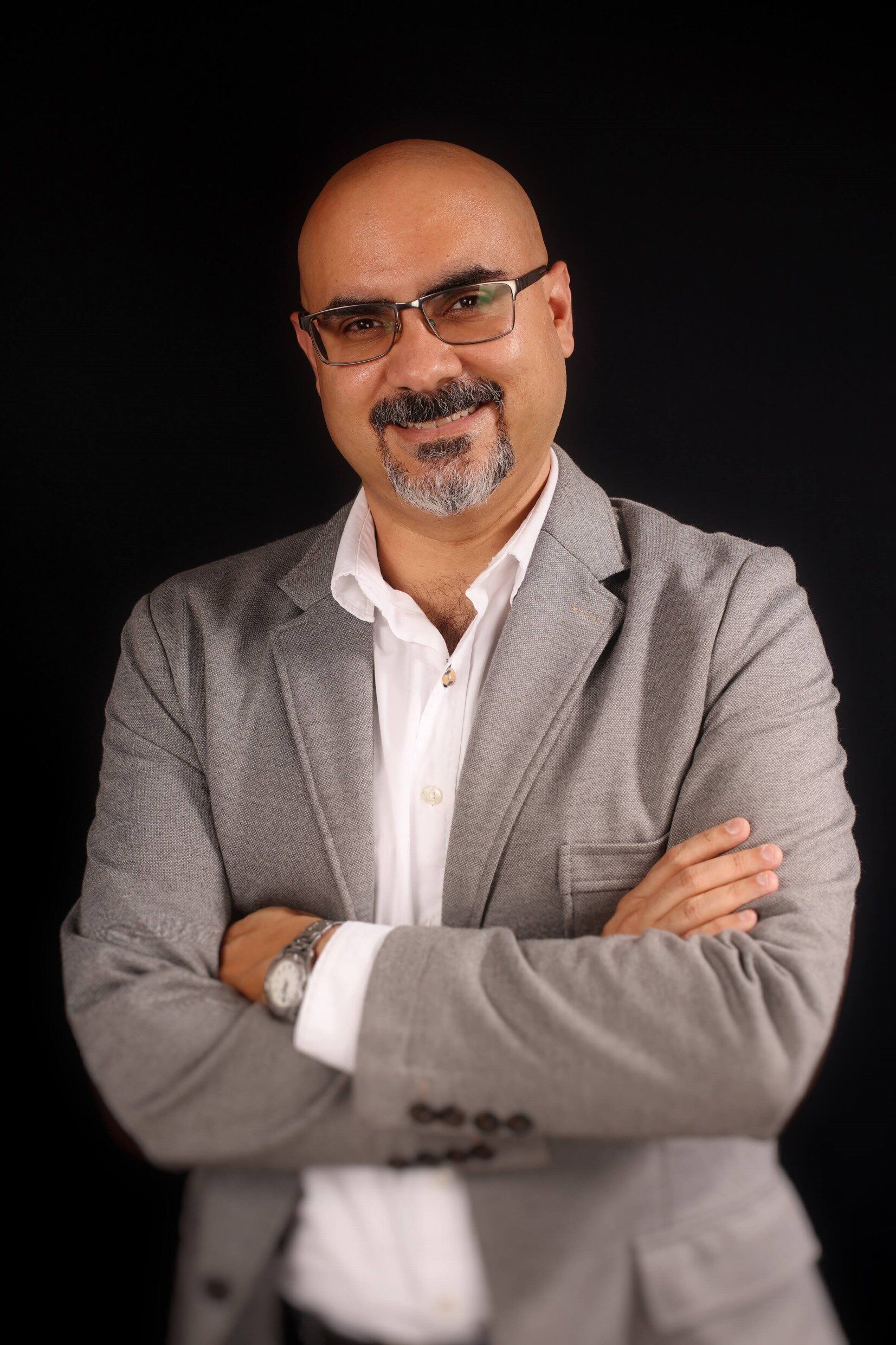
Ernesto Marquez
LEAD TECHNICAL CONSULTOR
WHY CHOOSE US?
“Baraka Consulting has delivered outstanding support to General Mills European operations by providing in-house technical expertise, in support of increased number of packaging projects and temporal unavailability of internal resources. Their consultants demonstrated a vast and deep technical mastery, responsibility and a true global exposure, that met and exceeded our expectations. Their expertise allowed a fast integration with the General Mills community and tools, minimizing the onboarding time which ensured fast results. In the initial phases of the collaboration Baraka Consulting demonstrated reactiveness, flexibility and competitiveness which was determinant to its selection as a partner of choice.”
— Orlando Fragoso, Global Packaging Technical Leader, General Mills.