Technical Outsourcing in Packaging: Advantages and Disadvantages
Explore the pros and cons of technical outsourcing in the packaging industry. Discover how outsourcing can enhance efficiency, reduce costs, and provide access to specialized expertise, while also considering potential challenges such as quality control, communication barriers, and dependency on external partners. Make informed decisions for your packaging needs by understanding the full spectrum of outsourcing implications.
Our Clients
We serve a wide range of clients and companies of different sizes, all across the world.
Technical Outsourcing in Packaging: Advantages and Disadvantages
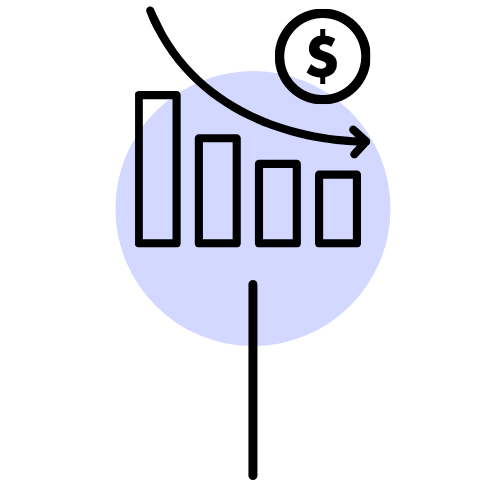
Product and Packaging
Maximization
We identify material and design standardization and optimization opportunities via benchmarking data and complexity analysis of your product, packaging and supply chain.
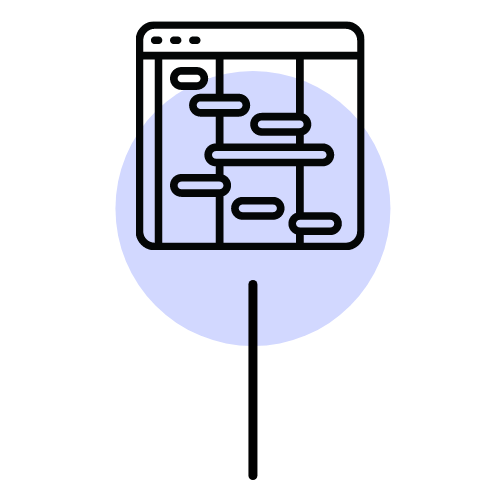
Technical Project Management
Our 15 years of experience in the consumer goods segment provides our clients first in class project management and technical mastery.
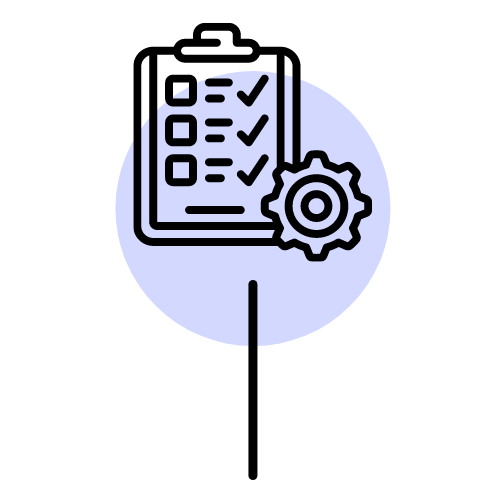
Standards and Quality Management Improvement
We help improve your technical specifications to drive more efficiency providing more control over quality systems.

Navigating the Pros and Cons of Technical Outsourcing in the Packaging Industry: A Strategic Guide for Long-Term Success
Navigating the pros and cons of technical outsourcing in the packaging industry requires a strategic approach to ensure long-term success. Outsourcing can offer significant advantages, such as cost savings, access to specialized expertise, and increased flexibility in scaling operations. By leveraging external resources, companies can focus on core competencies and accelerate innovation. However, it also presents challenges, including potential quality control issues, communication barriers, and dependency on third-party providers. To mitigate these risks, companies should conduct thorough due diligence when selecting outsourcing partners, establish clear contractual agreements, and maintain robust communication channels. Additionally, integrating a hybrid model that combines in-house capabilities with outsourced services can provide a balanced approach, allowing companies to adapt to market changes while maintaining control over critical processes. Ultimately, a well-planned outsourcing strategy can enhance competitiveness and drive sustainable growth in the packaging industry.
Strategic Outsourcing in the Packaging Industry: Balancing Benefits and Challenges for Sustainable Growth
Strategic outsourcing in the packaging industry has become an essential approach for companies aiming to enhance efficiency, reduce costs, and focus on core competencies. By partnering with specialized service providers, packaging companies can leverage advanced technologies, access skilled labor, and streamline operations, which can lead to improved product quality and faster time-to-market. Outsourcing also allows companies to adapt to changing market demands and regulatory requirements more swiftly. However, this strategy is not without its challenges. Companies must carefully select partners to ensure alignment with their sustainability goals and maintain control over critical aspects of their supply chain. Additionally, there is a risk of over-reliance on third-party providers, which can lead to vulnerabilities in the supply chain and potential loss of proprietary knowledge.
In conclusion, while strategic outsourcing offers significant benefits for the packaging industry, such as cost savings and operational efficiencies, it is crucial for companies to strike a balance between outsourcing and maintaining control over their core functions. By carefully selecting partners that align with their sustainability objectives and maintaining a robust oversight mechanism, companies can mitigate the risks associated with outsourcing. This balanced approach not only supports sustainable growth but also ensures that companies remain agile and competitive in a rapidly evolving market. Ultimately, the key to successful strategic outsourcing lies in fostering strong partnerships and continuously evaluating the impact of outsourcing decisions on the company's long-term goals.
WHY CHOOSE US?
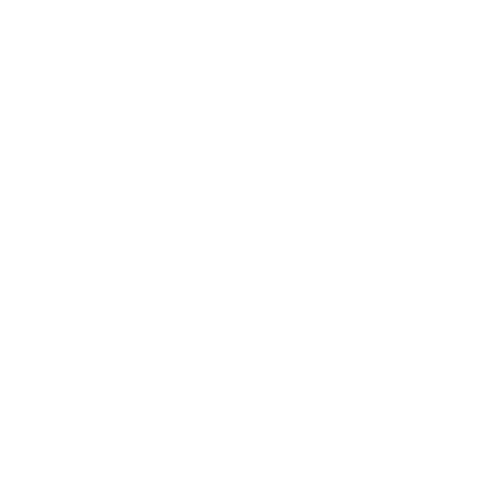
We analyze your product and packaging variables to create clear indexes on how you compare to your competition to help generate standardization and cost optimization options based on these findings.
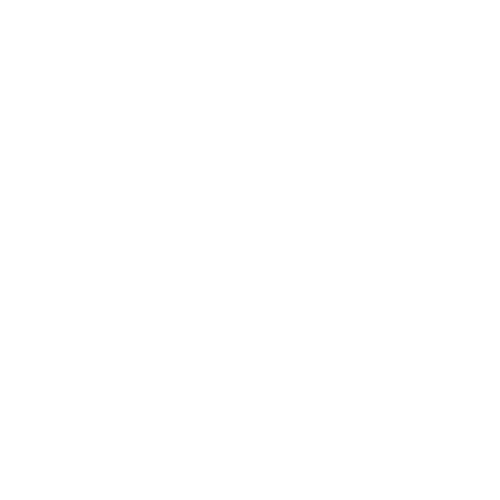
We help you to understand which are the best practices used inside your company and how your products and packages compare to the best practices in the market through external benchmarking.
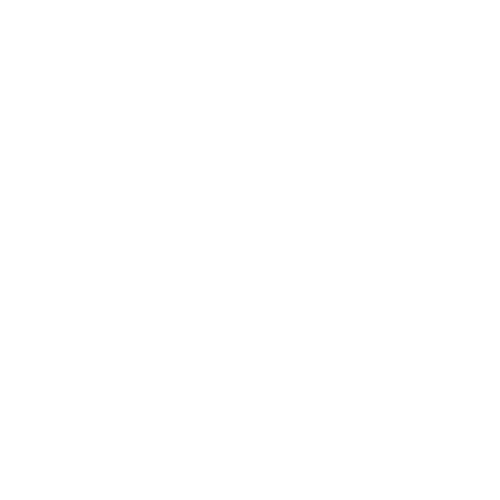
We focus on opportunities based on technical feasibility and size of the prize.
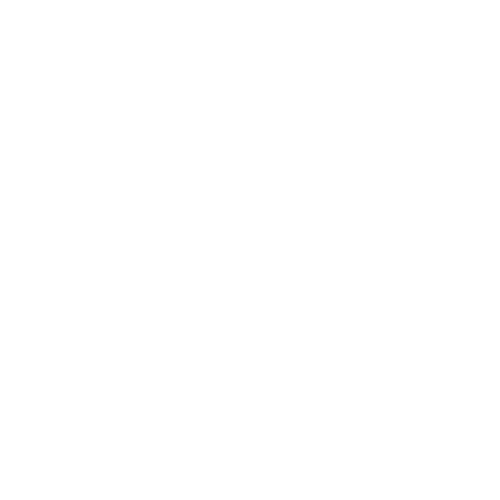
We have more than 15 years of experience working with consumer goods companies across different categories and regions. We provide access to a multi-functional team with technical mastery across different packaging and production platforms.
Meet Our Team
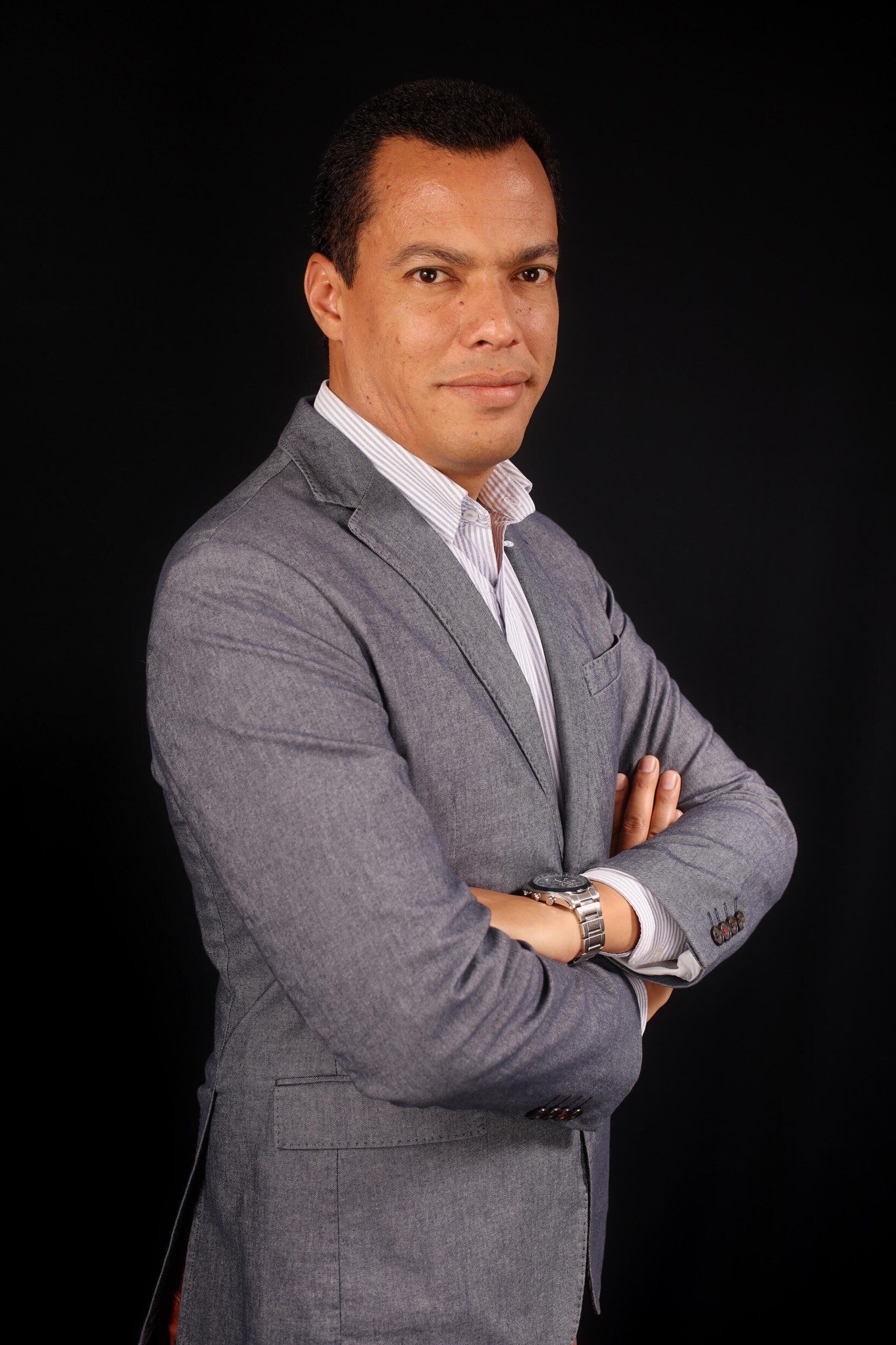
Victor Escalona
CEO AND CO-FOUNDER
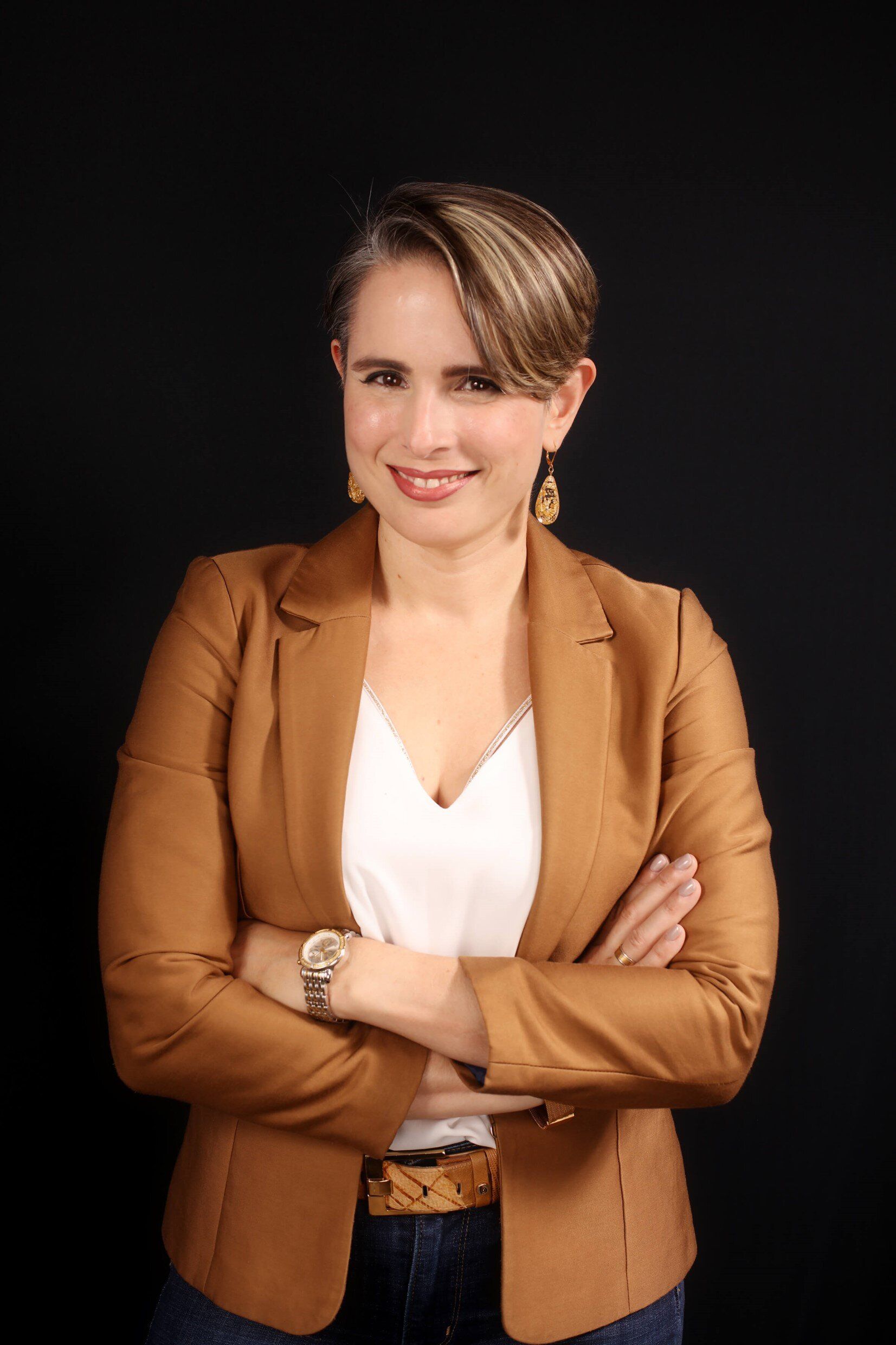
Carolina Chaparro
BUSINESS DELIVERY MANAGER AND CO-FOUNDER
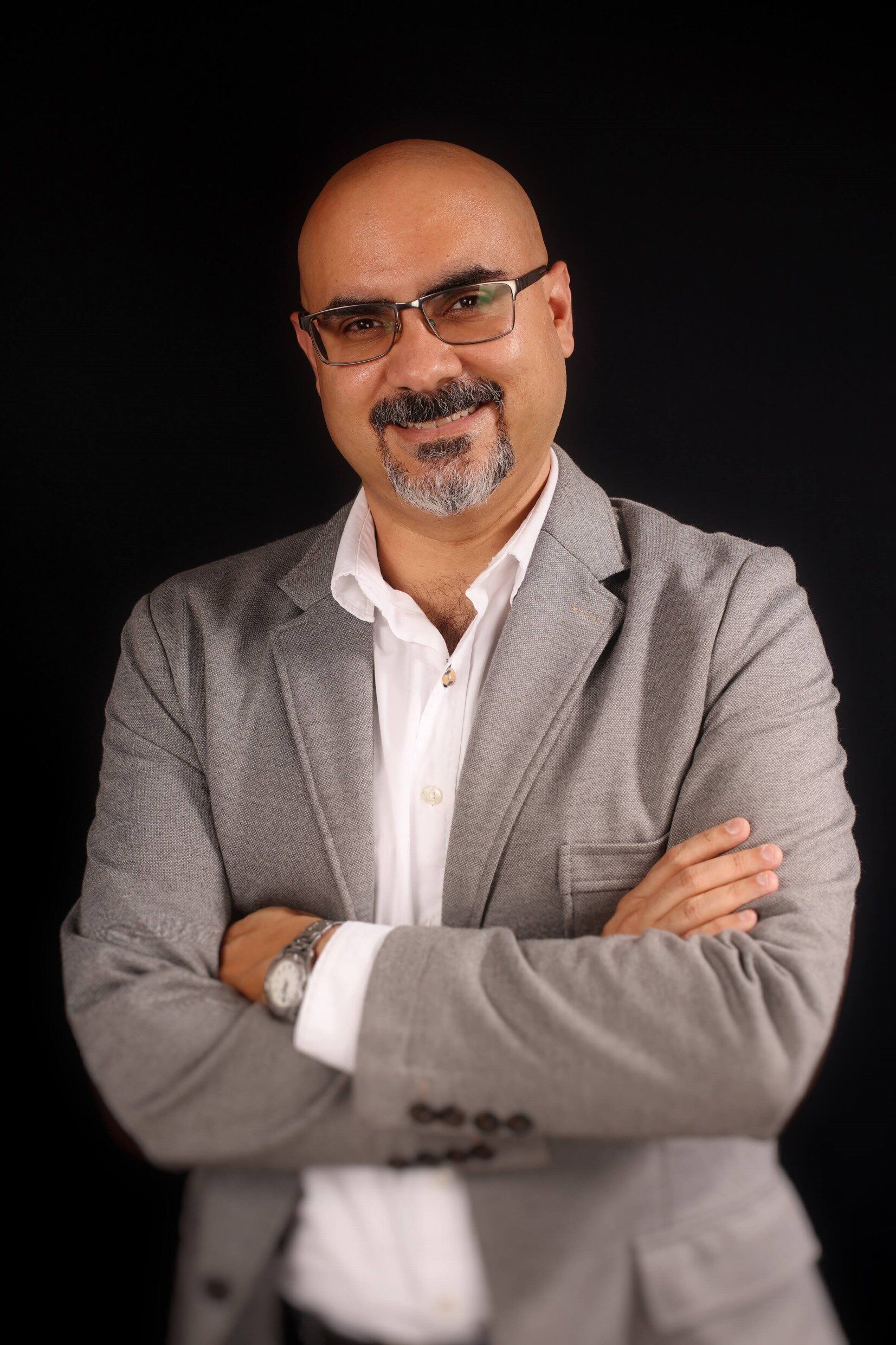
Ernesto Marquez
LEAD TECHNICAL CONSULTOR
WHY CHOOSE US?
“Baraka Consulting has delivered outstanding support to General Mills European operations by providing in-house technical expertise, in support of increased number of packaging projects and temporal unavailability of internal resources. Their consultants demonstrated a vast and deep technical mastery, responsibility and a true global exposure, that met and exceeded our expectations. Their expertise allowed a fast integration with the General Mills community and tools, minimizing the onboarding time which ensured fast results. In the initial phases of the collaboration Baraka Consulting demonstrated reactiveness, flexibility and competitiveness which was determinant to its selection as a partner of choice.”
— Orlando Fragoso, Global Packaging Technical Leader, General Mills.